hitechpipes
Electric Resistance Welded (ERW) Pipes: A Closer Look at Manufacturing and Applications
​
Electric Resistance Welded (ERW) pipes are a prominent category of steel pipes that play a vital role in various industries, including construction, infrastructure, and manufacturing. These pipes are known for their cost-effectiveness, durability, and versatility. In this comprehensive guide, we will explore ERW pipes, focusing on their manufacturing process, properties, advantages, and common applications.
​
​
​
​
​
​
​
​
​
​
​
​
​
​
​
​
​
​
​
​
​
​
1. What Are ERW Pipes?
Electric Resistance Welded (ERW) pipes are steel pipes produced by welding strips or coils of steel longitudinally. The process involves passing a high-frequency electric current through the edges of the steel strip or coil, heating it to the point where the edges melt and fuse together. The result is a seamless-looking pipe with excellent dimensional accuracy.
2. Manufacturing Process
The manufacturing process of ERW pipes can be summarized as follows:
-
Coil Preparation: Steel coils are unrolled and flattened to create a flat strip of steel.
-
Forming: The flat strip is shaped into a cylindrical shape, and the edges are pressed together to form a pipe.
-
Welding: High-frequency electrical resistance welding is used to join the edges of the pipe. This process involves passing an electrical current through the steel, heating it to the point of fusion, and forming a strong bond.
-
Sizing and Cutting: The welded pipe is then sized to the desired dimensions and cut to the required lengths.
-
Testing and Inspection: ERW pipes undergo various tests and inspections to ensure they meet industry standards and specifications.
3. Properties of ERW Pipes
ERW pipes exhibit several key properties that make them suitable for a wide range of applications:
3.1. Weld Quality
ERW pipes have high-quality welds, resulting in strong and reliable joints that can withstand various stresses.
3.2. Dimensional Accuracy
ERW pipes are known for their precise dimensions, making them ideal for applications where tight tolerances are required.
3.3. Straightness
ERW pipes are typically straight and have minimal bending or warping, ensuring ease of installation.
3.4. Smooth Surface
The welding process results in a smooth interior and exterior surface, reducing friction and improving flow in applications such as plumbing.
4. Advantages of ERW Pipes
4.1. Cost-Effective
ERW pipes are cost-effective compared to seamless pipes, making them a preferred choice for various projects.
4.2. High Production Efficiency
The manufacturing process of ERW pipes is highly efficient, allowing for the production of large quantities in a relatively short time.
4.3. Availability in Various Sizes
ERW pipes are available in a wide range of sizes, making them suitable for diverse applications.
4.4. Versatility
ERW pipes are versatile and can be used in various industries, including construction, plumbing, and manufacturing.
5. Common Applications
ERW pipes find widespread use in several industries and applications, including:
5.1. Plumbing and Water Distribution
ERW pipes are commonly used for water supply and plumbing systems due to their smooth interior surface and cost-effectiveness.
5.2. Construction and Infrastructure
In construction projects, ERW pipes are used for structural applications, such as building frames, scaffolding, and support columns.
5.3. Oil and Gas Industry
ERW pipes are used in the transportation of oil, gas, and other petrochemical products, where they offer a cost-effective solution.
5.4. Automotive Industry
ERW pipes are utilized in the manufacture of automotive components, including exhaust systems and structural parts.
5.5. Manufacturing
ERW pipes are employed in various manufacturing processes, including the fabrication of machinery and equipment.
6. Considerations and Challenges
While ERW pipes offer numerous advantages, they may not be suitable for all applications. Some considerations and challenges include:
-
Limited Use in High-Pressure Applications: ERW pipes may not be suitable for extremely high-pressure applications, where seamless pipes are often preferred.
-
Corrosion Resistance: Depending on the type of steel used, ERW pipes may require additional corrosion protection in certain environments.
7. Conclusion
Electric Resistance Welded (ERW) pipes are a valuable and versatile component in various industries, thanks to their cost-effectiveness, precision, and efficiency. The manufacturing process ensures strong welds and precise dimensions, making them suitable for a wide range of applications. Whether used in plumbing systems, construction projects, or the transportation of critical resources like oil and gas, ERW pipes play a vital role in building and maintaining the infrastructure that powers our modern world.
More Read: Steel pipe | ERW Pipes
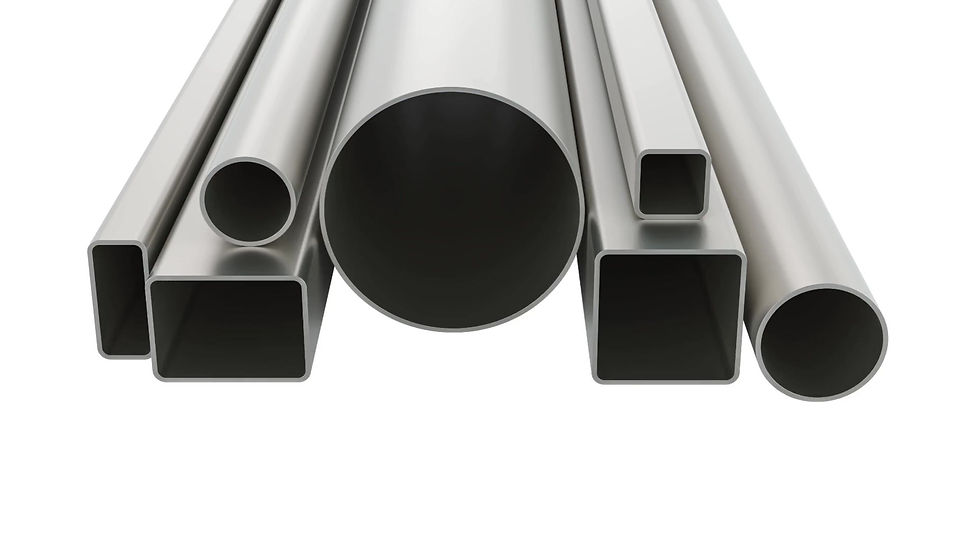